Silicon wafer disc grinder; Jig borer series; Vertical machining center; Rapid prep flap discs.
The Helical SN8-13 milling system features double-sided helix inserts with eight cutting edges that lower cost per edge to boost slotting, side milling, and circular rough milling efficiency. Felt Polishing Flap Disc
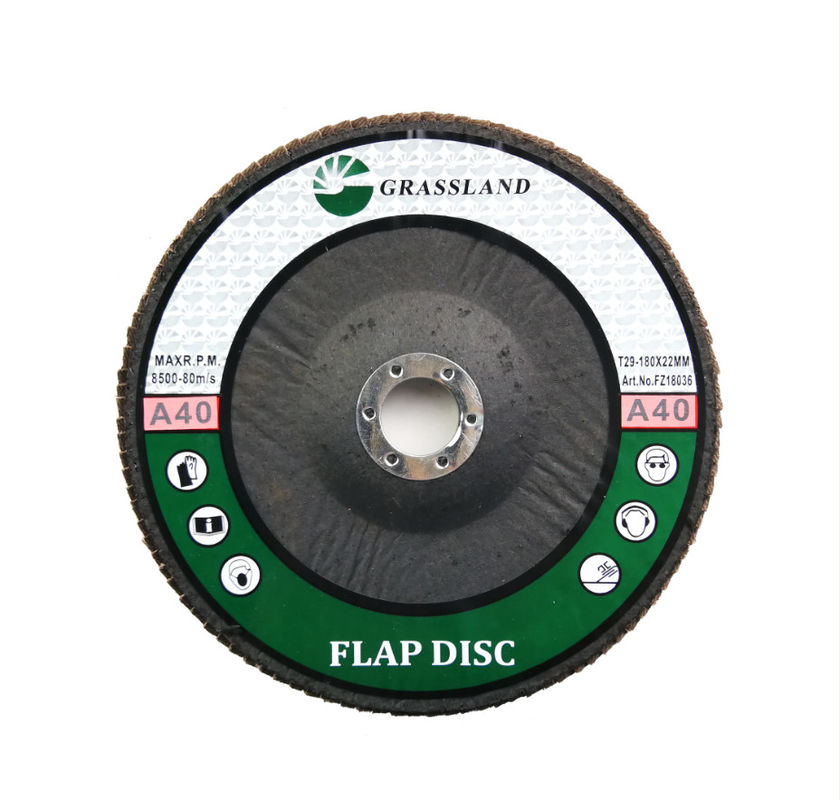
For applications involving ISO P, M, K, and S materials, the cutters offer application-specific subfamily designs featuring left- or right-hand helixes, half- or full- effective teeth options, two front inserts, and many radii choices for longer tool life and maximum chip evacuation. The Helical SN8-13 also eliminates incorrect indexing of front and helix inserts, reducing operator error.
As an alternative to milling products for depths-of-cut from 50mm up to 100mm (2" up to 3"), Seco offers the Helical SN8-13 in a range of subfamilies built with its SN13 helix inserts.
The DXSG320 double-disc horizontal grinder simultaneously grinds both sides of silicon wafers to ±1µm from as-sliced condition. The DXSG320 performance represents improvement in accuracy and productivity compared to the single-spindle vertical grinders common in the chip industry which grind to 3µm to 4µm.
A further advantage of the DXSG320 grinder is the footprint is approximately 20% smaller than other machines while including fully automated work handling internal to the machine. Wafers are put into a fixture and loaded into a rack system to carry the wafers into the machine for sizing and finishing to customer specifications.
To assure correct stock removal and optimum quality, wafer thickness is measured before and after grinding. During grinding, discs float in the fixtures and spin during the grinding process, resulting in rapid, even material removal. Since there’s no need to flip over the part during the grinding process, users save considerable cycle time.
Key features of the grinder include a GW high-frequency spindle with air static pressure and a built-in motor to achieve high-speed, high-accuracy grinding. In-process, wheel positioning is automatic through high-accuracy air gauging. The use of pure water instead of coolant is environmentally friendly. The machine is compatible with a variety of data collection systems through easy-to-use communication software.
The J12/J/16 jig borer series combines large capacity and high precision for accurately machining workpieces such as molds and castings. The machines offer Y-axis stroke of either 1,250mm or 1,600mm, with standard table sizes of 2,400mm x 1,250mm or 2,900mm x 1,600mm.
The machines’ strong, durable structures provide table lateral movement accuracy of 2.5µm or better. The Z-axis guide system is restrained on four sides to maximize rigidity and reliability while dual ballscrews ensure stable feed motion.
For precision holemaking applications, X-Y interpolation enables the J12/J16 machines to perform high-precision contouring by using an end mill instead of a boring tool, eliminating the need to manually adjust a boring tool to accurately finish the hole diameter. Pitch accuracy is within 5µm even for large-pitch holes.
The machines feature a 12,000rpm 50 taper spindle and automatic tool-change capacity of 60 tools. Additional options such as quill spindle, increased work capacity, and automation features are available to meet customers’ needs.
A 5-axis vertical machining center (VMC) with a solid double-column structure combines power and productivity for high- precision machining in a compact design.
The GENOS M560V-5AX evolved from two Okuma VMCs – the GENOS M560V and the GENOS M460V-5AX, which launched in 2017 as an answer to a market need for an affordable, compact 5-axis VMC, without compromising the design or accuracy.
The GENOS M560V-5AX offers a working envelope with a 500mm table and axis travels of 1,050mm, 560mm, 460mm, (X, Y, Z) while still maintaining a compact footprint. Further optimizing the machine’s design is a trunnion table positioned parallel to the front of the machine which allows for easier access to the table and good visibility during machining. This, and other user-friendly features on the machine, reduce physical burden on the operator. The machine comes standard with a 60 capacity automatic tool changer (ATC) magazine and can also accommodate tools measuring up to 400mm in length.
The GENOS M560V-5AX comes standard with Okuma’s Thermo-Friendly Concept, an on-board thermal and energy management technology to support stable, high-accuracy machining and reduce energy consumption.
Vortex Rapid Prep Non-Woven Flap Discs last longer, producing increased cutting rates and smear-free finishes. Vortex agglomerated aluminum oxide grain technology enables the cutting power of a coarser grit while producing a finer finish in one abrasive disc solution. The non-woven discs can increase material removal rates (MRR) more than 50% compared to non-woven medium grit flap discs.
For light blending, stripping, edge breaking, and surface prep applications, the flap discs feature special three-dimensional non-woven abrasive layers. This design ensures uniform finishing with a consistently low surface finish value. Multiple layers of surface conditioning material provide added life, fewer disc changes for better efficiency, and reduced vibration. The discs also feature Clean Bond resin technology for smear-free finishes, even on high nickel content alloys, and reduced loading when cutting aluminum and other softer metals.
Vortex Rapid Prep Type 27 Discs also provide forgiveness and reduced vibration on uneven surfaces for maximum ergonomic use. Discs are offered in 4-1/2ʺ x 7/8ʺ and 4-1/2ʺ x 5/8ʺ-11 sizes in fine, very fine, medium, and coarse grits.
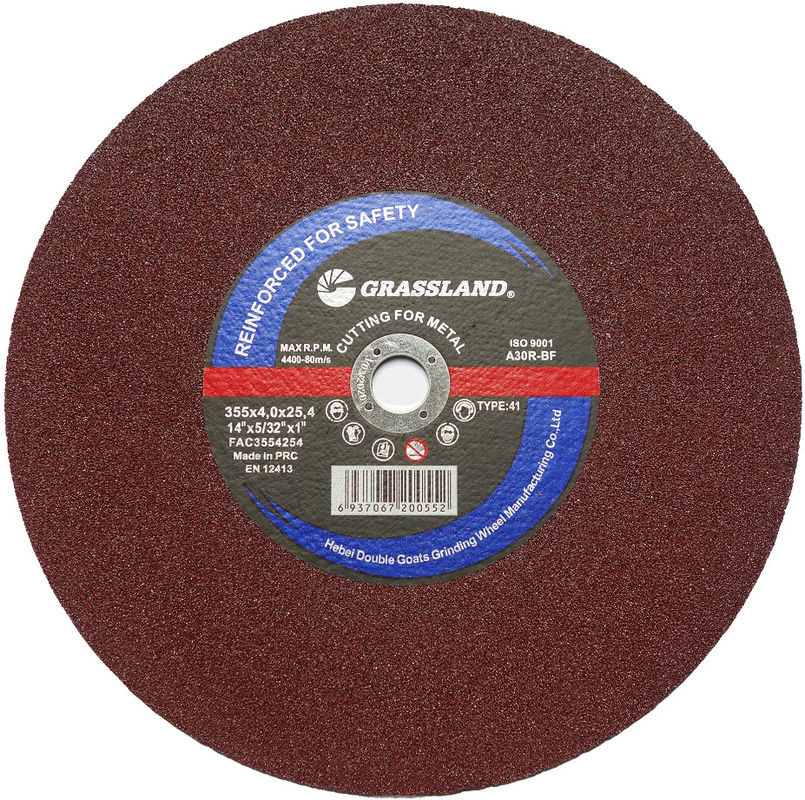
Polishing Flap Disc For Angle Grinder Check out more from this issue and find you next story to read.